유효 전력 사이클링을 이용한 전력 모듈의 실제 수명 예측
- Delta ES_Lee, Seol.
- 2021년 12월 10일
- 8분 분량
개요
전력 전자 모듈과 전력 패키지 설계는 열 문제에 크게 영향을 받습니다.
해당 모듈의 열 저항을 낮추기 위해 새로운 기판 소재와 더 얇고 높은 열 전도율의 부착 소재가 사용됩니다.
새 소재나 기술을 적용할 때는 모듈의 생산을 고려하기 전에 철저한 신뢰성 시험을 거쳐야 합니다.
모듈의 안정성이나 예상 수명은 시스템이 견딜 수 있는 온도 또는 전력 사이클 수로 나타낼 수 있습니다. 하지만 이는 전력 모듈이 실제 적용 환경과 예상 수명이 연관될 경우 좀 더 정확하며, 전력 모듈 설계가 신뢰성과 가격, 무게, 부피 등의 요소들 간 절충에 따른 적용 환경에 따라 결정되므로 이러한 요소들을 최소화하면서 적용 환경을 고려한 높은 수준의 신뢰성을 가진 필요 수명 보장이 목적이 되어야 합니다.
이 백서에서는 설계자가 부품의 적용 환경을 고려하면서 전력 모듈의 예상 수명을 예측하는 데 유효 전력 사이클링 측정법이 어떻게 도움이 되는지에 대해 설명합니다. 관련 개별 단계가 요약되어 있습니다.
서론
IGBT 또는 MOSFET 등의 전력 전자 모듈이 자동차, 철도 견인, 발전 및 변전 등의 응용 부문에서 점점 더 광범위하게 사용되고 있습니다. 이 응용 부문에서 이러한 패키지의 가장 중요한 설계 요구 사항은 고장 수명입니다. 높은 신뢰성과 안전을 중요시하는 전력 전자 모듈 적용에는 모듈의 적용과 적용 환경이 장시간 지속되는 것을 요구합니다.
고장의 주요 요인은 다양한 소재의 서로 다른 열 팽창 계수로 인해 구조 내에서 발생하는 열-기계적 응력입니다. 이러한 응력은 모듈 내 온도 변화에 의해 유도되며, 온도 변화는 장치가 노출되어 있는 가변 전력 프로필로 인해 발생합니다. 전력 모듈의 다양한 부품 내 온도 변화와 변화 비율 변동은 주요한 고장 메커니즘의 가속화 요인들입니다. 여기에는 기초판 납땜의 균열 같은 열 전도 경로의 열화와 결합선의 열화가 포함됩니다. 열적 유도 고장을 최소화하는 가장 쉬운 방법은 패키지의 열 저항을 최소화하여 작동 중 접점 온도 이상을 제한하는 것입니다. 모듈의 열 저항은 열 과도 테스트를 통해 평가할 수 있습니다. 이 테스트를 통해 패키지에 대한 총 열 저항뿐만 아니라, 다이에서 기초판까지 열이 전달될 때 확산되는 저항을 포함하여 구성 부품의 부분 열 저항도 확인할 수 있습니다.
가속화 테스트 전략
전력 모듈에 대해 일반적으로 사용하는 두 가지 수명 테스트는 온도 사이클링과 유효 전력 사이클링입니다. 두 테스트 방법 모두 장치 온도를 주기적으로 변경하여 열 부하를 발생시키지만 기본적으로는 다릅니다. 온도 사이클링에서는 장치에 전원이 공급되지 않습니다. 온도 변화는 오븐과 같은 온도 조절 환경에 부품을 놓고 부품을 가열했다가 냉각하는 방식으로 이루어집니다. 따라서 가열이 외부적으로 적용됩니다. 가열 및 냉각 속도가 매우 느린(몇 분 소요) 편이므로 부품 내 온도가 가열 및 냉각 시 아주 균일하게 유지됩니다. 온도 사이클링은 구리 직접 접합(Direct Bonded Copper, DBC) 기판과 모듈의 기초판 사이 납땜 접합부를 평가하는 데 주로 사용됩니다.
이와는 달리, 유효 전력 사이클링 방법에서는 반도체 장치를 통해 전류를 전달하여 이러한 장치를 소산 소자로 사용함으로써 부품이 내부적으로 가열됩니다. 열이 일반 작동 중에 손실되는 것과 동일한 위치에서 손실되므로 부품 내 온도 분포가 적용 부문과 비슷합니다. 가열이 국부적이므로 온도 구배도가 상당히 큰 편입니다. 이러한 온도 구배는 공급 전류를 변경하여 가열 속도를 변경함으로써 제어할 수 있습니다. 유효 전력 사이클링에서는 낮은 전류와 긴 가열 및 냉각 시간을 사용하여 DBC와 모듈 기초판 사이 납땜 접합부를 가열할 수도 있습니다. 일반적으로 유효 전력 사이클링은 가열 시간이 단 몇 초에 불과한 짧은 사이클 타임을 사용합니다. 높은 전류는 결합선과 다이 부착 납땜 접합부에 응력을 가하여 칩 접점 온도를 평가하는 데 사용됩니다.
그러므로 유효 전력 사이클링을 사용하면 패키지의 장기 신뢰성을 포괄적으로 검사할 수 있습니다. 열 구조 내 온도 변화로 다양한 유형의 열화가 발생하므로 각 사이클마다 컬렉터-이미터(배출 소스) 전압 강하나 게이트 누출 전류 같은 전기 파라미터에 대한 영향을 관찰할 수 있습니다.
과도 열 테스트를 주기적으로 실시하여 열 스택 저하도 모니터링할 수 있습니다. 두 방법의 결합을 통해 신뢰성 엔지니어가 모듈 내 다양한 연관 고장 메커니즘의 발생을 완벽하게 평가할 수 있습니다.
수명 예측에 대한 접근 방법
장치의 동작 주파수에서는 유효 전력 사이클링 테스트를 수행할 수 없습니다.
고속 스위칭 중에는 저하과정에 영향을 받는 파라미터를 정확히 측정할 수 없습니다. 더 큰 문제는 테스트 대상 부품이 작동 상태에 있으므로 테스트 시간을 거의 가속화할 수 없는 범위에서 수명 테스트 자체가 부품의 예상 수명에 근접할 것이라는 점입니다. 하지만 이러한 테스트를 사용하여 부품이 응용 환경에서 접하게 될 접점 온도 변화의 비율과 정도를 파악할 수 있습니다.
일반 작동 중에는 전력 전자 장치 스위칭 주파수가 일정합니다. 하지만 부품이 켜진 상태의 사이클 비율(충전율)은 각기 다릅니다. 부품이 꺼진 상태에서는 전력이 손실되지 않습니다. 스위칭될 때(켜지거나 꺼짐), 스위칭 주파수에 따라 서로 다른 스위칭 손실이 발생하며, 켜진 상태에서는 일정 전도 손실이 더 낮습니다. 구조의 열적 관성으로 인해 사이클 내 열 손실 변화의 영향은 무시해도 되는 수준이며, 사실상 이러한 열 구조는 사이클 전체의 시간 평균 열 손실량을 나타냅니다.
이러한 정보에 기초하여, 장치를 열고 장치에 정전류를 가함으로써 전도 손실을 사용하여 작동 시 발생하는 시간 평균 가열을 재현하는 방식으로 부품을 테스트할 수 있습니다. 더 높은 전류를 가하고 전원 공급 및 전원 차단 시간을 조정하여 원하는 접점 온도 변동을 유도함으로써 이 테스트를 가속화할 수 있습니다.
최종 적용 부문의 기대 수명을 예측하는 일은 복잡한 작업입니다. 이 작업을 수행하려면 작동 사용률, 즉 '미션 프로필(mission profile)'을 알아야 합니다. 이 정보를 알고 있으면 '전력 프로필'(선택 사항)을 계산할 수 있으며, 전력 프로필은 모듈을 설계 대상 장비 내 원하는 작동 상태로 유도하는 데 필요합니다.
입력 전력 프로필과 패키지의 기계적 구성 및 대상 열 환경을 올바르게 파악했으면, 과도 열 시뮬레이션을 통해 최종 시스템 작동 중에 장치 접점의 온도 변화를 예측할 수 있습니다. 다양한 온도 변화는 패키지의 수명에 서로 다른 영향을 미칩니다. 사전 설정된 접점 온도 변동 수에서 수집된 유효 전력 사이클링 데이터에 근거하여 ‘수명 곡선’을 정확히 작성할 수 있습니다.

그림 1. 전체 시스템 고장 시간 예측 과정
과정 설명 전력 모듈의 수명은 포함된 장치(IGBT, MOSFET, 다이오드 등), 패키징 설계, 제조 및 다양한 외부 요인에 따라 달라집니다. 장치가 견뎌야 하는 모듈의 열-기계적 설계와 환경 조건(온도, 습도 및 진동) 외에도, 장치 자체에서 발생하는 열과 냉각 시스템의 특성은 수명을 결정하는 가장 중요한 두 가지 요인입니다. 미션 프로필 정의 모듈의 표준 부하를 설명하려면 모듈이 수명 시간 동안 반복적으로 수행해야 할 특수한 특성 작업을 설명해야 합니다. 미션 프로필은 일반적으로 모듈에 발생하는 부하와 직접적으로 관련된 변수의 시간 함수입니다. 가장 간단하지만 거의 사용하지 않는 미션 프로필 P(t)는 IGBT 모듈의 각 장치에 대한 시간 함수로 표현되는 전력 손실입니다. 이 미션 프로필은 추후 계산에 직접 사용할 수 있습니다. 미션 프로필을 전체 시스템 상태의 시간 함수로 정의하고 나서 시스템의 기계 및 전기 모델을 사용하여 P(t)를 계산하는 것이 보다 일반적입니다. 자동차 업계의 차량 관련 일반 사용 사례에서는 표준 연비 테스트용으로 시간 대비 속도 프로필이라고 하는 v(t)가 정의되어 있습니다. 미국 환경보호국의 도시 동력계 주행 계획(Dynamometer Driving Schedule, UDDS) 주행 프로필은 경량 차량의 도시 주행 조건을 나타내는 데 사용됩니다. 그림 2에는 이 프로필이 나와 있습니다.
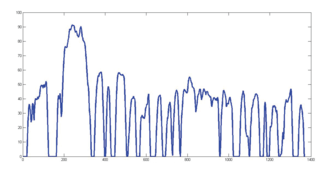
그림 2. 도시 동력계 주행 계획(Urban Dynamometer Driving Schedule, UDDS)
전기 차량의 기계 모델에 근거하여, 전기 모터의 부하와 주행 회로의 최종 전력 손실을 계산하여 P(t) 프로필을 제시할 수 있습니다. 열 부하 결정 전력 모듈의 가장 일반적인 고장 원인은 주기적 사이클링에서 발생하는 열적 유도 응력으로 인한 다양한 층의 균열이나 박리입니다. 열 응력의 크기는 반도체 장치에서 손실되는 전력에 의해 유도되는 온도 변화에 비례합니다. 따라서 다음 단계는 P(t) 미션 프로필을 시간 대비 온도 함수로 변환하는 것입니다. 손실이 일정하지 않고 복잡한 시간 함수로 표현되므로 온도 함수를 분석적으로 계산할 수 없습니다. 대부분의 현대식 3D 열 시뮬레이터는 과도 시뮬레이션을 수행할 수 있으며, 임의 손실 프로필을 처리할 수 있는 시뮬레이션도 있습니다. 상당히 복잡한 패키지 구조의 경우라도 그림 3에서처럼 정밀 3D 모델을 설계할 수 있습니다.

그림 3. FloTHERM XT의 IGBT 상세 열 모델
시뮬레이션 모델을 사용하여 신뢰성 연구에 적용하려면 과도 동작이 실험 결과와 정확히 일치하도록 보정해야 합니다. 실험 중 수명에 영향을 미치는 파라미터에 대한 정확한 제어는 매우 중요하며 과소 평가해서는 안 됩니다. 그림 4는 사이클 타임 동안 접점 온도 변화를 제어하기 위한 동일 IGBT 샘플에 대한 유효 전력 사이클링 테스트를 보여 줍니다. 접점 온도가 110°C에서 120°C로 변경될 때(a 9% 증가), 수명은 ~57500회 사이클에서 ~39000회 사이클로 단축되었습니다(a ~37% 감소).

그림 4. 사이클링하에서 접합점 온도 변동의 10도 차이에 따른 IGBT 수명
수명은 접점 온도 변동에 크게 영향을 받으므로 시뮬레이션 모델을 수명 예측에 사용해야 하는 경우 부하 프로필 P(t)에 따른 접점 온도 변동을 높은 정확도로 예측할 수 있어야 합니다. 칩 패키지의 높은 정확도 열 모델을 설계할 때 중요한 문제는 모델의 구성 소재, 결합부 또는 납땜부 두께(다이 부착 층)과 같은 열적 특성을 포함해야 하는 것입니다. 결과적으로 전력 단계에 대해 시뮬레이션된 열 반응은 실제로 관찰되는 것과 다릅니다. 이 모델을 정밀 보정하려면 매우 정확한 테스트 데이터가 필요하며, 온도와 시간 분해능이 높으면 온도 시간 응답을 구조 함수로 변환하여 열 유동류 경로에 따라 열 저항 대비 누적 열 용량을 나타낼 수 있습니다. 그림 5는 FloTHERM [10]의 IGBT 열 응답과 Mentor Graphics의 T3Ster 열 특성화 하드웨어인 T3Ster로 측정한 물리 부품의 열 응답을 비교한 것으로, 왼쪽은 모델의 초기 설정이며 오른쪽은 보정 이후입니다. 패키지 내 열 유동류 경로를 따르는 모든 시간 상수가 올바르고, 적용된 열 펄스의 길이와 관계없이 온도 상승이 올바르게 예측되도록 하려면 곡선의 모든 부분이 정확히 일치해야 합니다.
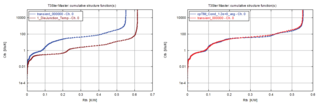
그림 5. 모델 보정 전/후의 IGB 구조 기능
그림 6은 T3Ster에서 생성된 구조 함수를 사용하여 보정한 후 구조의 상세 모델을 사용한 열 시뮬레이션에서 얻은 IGBT 모듈 내 단일 칩의 온도-시간 함수를 부분적으로 보여 줍니다.
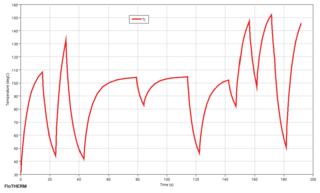
그림 6. 해당 전력 플필에 대한 시뮬레이션 된 IGBT 칩 온도
모듈 내 칩의 접점 온도에 해당하는 온도 곡선이 생성된 후에는 함수의 국부적 최소 및 최대 값을 식별하여 온도 변화를 계산해야 합니다. 각 온도 변화도(±0.5°C 이내)의 발생 횟수를 계산하여 분산 상태를 히스토그램으로 표현합니다. 예제 히스토그램이 그림 7에 나와 있습니다.

그림 7. 접합점 온도 변동 히스토그램
히스토그램은 두 가지 역할을 합니다. 첫 번째, 전력 사이클링 테스트 시 파라미터 선택에 도움을 줍니다. 두 번째, 총 온도 변동 수별로 각 온도 사이클 변화 발생 수를 정규화하면 나중에 총 수명 계산에 사용할 수 있도록 다양한 온도 변화 크기에 대해 가중치를 부여할 수 있습니다. 모듈 수명 곡선 위의 섹션에서는 계산과 시뮬레이션을 사용하여 온도 변화가 장치에 어떻게 응력을 가하는지 살펴보았습니다. 특정 부하에서 장치의 수명을 살펴보려면 Mentor Graphics의 MicReD Industrial Power Tester 1500A 같은 장비를 사용하여 실제 수명을 테스트하는 방법이 최선입니다. 임의 고장의 영향을 배제하고 올바른 수명 곡선을 계산하려면 통계적으로 유의한 양의 데이터가 필요합니다. 따라서 상당수의 실험을 실시해야 합니다. 수명 실험은 시간이 많이 드는 작업이므로, 테스트 파라미터를 신중히 선택하고 전체 테스트 기간 동안 정확히 유지해야 합니다. 온도 변동, 도달한 최대 온도 및 사이클 기간 등은 가장 중요한 파라미터 입니다. 장치 고장이 발생할 때까지 전력 사이클링이 계속되어야 합니다. 테스트의 결과로, 특정 테스트 파라미터 세트에 대한 장치 고장 시점까지 경과된 사이클 수(Nf)가 산출됩니다. 가능한 모든 부하 조건에서 장치를 테스트하는 것은 실제로 불가능하지만, 특정 수의 부하에서 장치를 테스트하여 커브 피팅에 의해 다른 모든 부하에 대한 수명을 예상할 수 있습니다(그림 8).

그림 8. 실험 결과 및 해당 고장 모델
고장 모델 개발 보다 다양한 파라미터를 고려하는 여러 모델이 있지만, 이러한 모든 모델의 기본은 기본적으로 화학 반응 속도를 표현하기 위해 정밀하게 고안된 유명한 Arrhenius 모델입니다.

여기서 Ea는 활성화 에너지, kb는 Boltzmann 상수, 그리고 T는 절대 온도입니다. 이 공식에서는 평균 온도만 고려합니다. 온도 변동이 클수록 수명이 단축된다는 경험적 사실을 고려하여, ΔTj 조건을 공식에 추가하면 열-기계 응력 모델이 산출됩니다.

여기서 ΔTj는 접점 온도 변화이며 A와 α는 커브 피팅을 사용하여 계산되는 계수입니다.
이 모델이 고장률에 대한 상당한 근사치를 제공할 수 있음에도 불구하고, 사이클 타임 역시 수명에 영향을 미칩니다. 짧은 고전력 가열 펄스 방식이나 긴 저전력 가열 펄스 방식으로 동일한 접합점 온도 변화를 실현할 수는 있지만, 선택한 방식에 따라 수명이 달라집니다. 가열 전력이 높으면 시간이 충분하지 않아서 패키지의 일부 기능이 이 짧은 시간 동안 가열되지 않습니다. 가열 펄스가 짧으면 기본적으로 칩 자체, 다이 부착 및 선 결합에 응력이 가해집니다. 가열 전력이 낮아서 동일한 온도 변화를 발생시키는 데 더 긴 가열 시간이 필요한 경우 열이 DBC 기판과 기초판으로 분산되므로, 위의 방식과 마찬가지로 동일한 접합점 온도 변동을 발생시킴에도 불구하고 패키지 내 온도 분산 변화가 크게 달라집니다.
그러므로 긴 펄스는 접합점에서 먼 쪽으로 납땜층에 응력을 가합니다. 이러한 사실을 고려하여 추가 조건인 fβ를 위의 공식에 추가하면 Norris-Landzberg 모델이 산출됩니다.

여기서 f는 사이클 타임이며 β는 곡선 적합을 사용하여 계산된 또 다른 계수입니다. 전력 모듈을 제조하는 일부 회사(해당 업체의 응용 지침 중 하나에서)에서 이와 유사한 모델을 사용하는 것으로 보고되었습니다. Infineon은 수명 모델링에 대해 이와 유사한 식을 사용하는 계산을 게시했으며, 단지 전체 사이클 기간 대신에 가열 시간만을 고려한다는 점이 달랐습니다. 관련 문헌에는 훨씬 더 다양한 파라미터(예: 전기 부하 조건: 전류와 전압)를 고려하는 보다 복잡한 모델도 제시되어 있으나, 이들 파라미터가 작동 중에는 조절되지 않고 안정성 테스트 중에만 조절될 수 있으므로 해당 모델의 예측 정확도를 높일 수 없습니다.
사용 수명 계산
이전 섹션에서는 실험적 전력 사이클링 결과에 기초하여 장치 수명을 모델링하는 방법을 살펴보았지만, 결과적으로 Nf 수명은 특정 일정 부하(계산된 시점)에서만 장치 수명을 예측합니다. 장치의 예상 총 수명을 계산하려면 선택한 미션 프로필에 따른 가변 부하를 고려하여 서로 다른 부하 조건의 전반적인 영향을 예상해야 합니다. 동시에 발생하는 다양한 부하로 인한 에이징 영향을 합산하는 데 일반적으로 사용되는 공식은 다음과 같습니다.

여기서 Nf_sum은 예상 고장 발생 시점까지 미션 프로필에 해당하는 부하를 장치에 적용할 수 있는 횟수이며 wi는 히스토그램에서 계산된 가중치입니다. 마지막으로, 이 합산된 사이클 수 Nf_sum에 미션 프로필 기간을 곱하면 작동 수명을 계산할 수 있습니다.

결론
미션 프로필 기반 전력 모듈 설계는 전력 전자 산업에서 최신 설계 방법으로 사용되고 있습니다. 열 시스템의 수명을 정확히 예측하려면 미션 프로필, 시스템의 기계 속성, 사용된 전력 모듈의 안정성 특성 같은 여러 파라미터를 알고 있어야 합니다.
이러한 파라미터의 정확한 정의와 열 모델 보정을 결합하면 수치적 방법을 사용하여 전력 장치 접점의 온도 변화를 올바르게 계산할 수 있습니다. 그러고 나면 이 정보를 수명 곡선 데이터와 결합하여 올바른 수명을 예측할 수 있습니다.
해당 미션 프로필에 근거하여 시스템의 수명을 예측하는 방법은 전력 모듈 설계자에게 예상 고장 시간에 대한 높은 확신을 제공하여 신제품 도입을 지원할 뿐만 아니라, 비용 절감의 이점을 제공하여 새로운 응용과 냉각 솔루션을 이용할 수 있게 합니다.
Comments